So, like we wrote last Monday, we are visiting Seeedstudio in Shenzhen, China. It’s been a great visit and we have gotten a chance to see both the Seeedstudio offices, the production and a bit of Shenzhen. And of course we also got a chance to do some shopping at the local markets. If you ever happen to find yourself in Shenzhen make sure to drop by the SEG Electronics Market, it’s a great place for electronics enthusiasts such as us!
Since we had some problems getting vacation all at once from our employers we decided to travel separately and overlapping each other a bit. Tobias left first and then me and Arnaud a couple of days later. After roughly 22 hours of travel we landed in Hong Kong and took the bus/train to Lo Wu to the Chinese boarder. Since I went traveling the week before and I couldn’t send my passport for the visa application we took the chance that we could apply for one at the boarder (after reading about it online). Turn out that it’s very easy to get a visa for the Shenzhen area (not all of China) at the boarder at Lo Wu. Took about 5 minutes and cost between ~130 yen. Just note that it’s not all nationalities that this applies to and the rules seem to change every once and a while.
Meanwhile Tobias spent his time visiting Seeedtudio and got to see the production. All the PCB assemblies was already done but the testing was running full speed. We use a simplified bed of nails test-jig that does the programming and tests voltages, current, battery charging, motor drivers etc. It is working very well and every Crazyflie plus Crazyradio takes about 2 minutes to program and test.
Visiting at Seeedstudio was great! We have been mailing and talking on Skype for the last 18 months with lots of people there and it was great to finally meet them in real life. Of course we got a guided tour around their offices which seems like a great place to work, lots of electronics everywhere :-) We also got a chance to catch up on the progress for the production. There’s lots of practical problems to solve when we scale up from only doing prototypes to full production, such as test-rigs for the Crazyflie.
After doing some research online we decided to head for the SEG Electronic Market to check it out and do some shopping. Inside it’s like a bazaar filled with small corridors and little booths selling all kinds of stuff. And this continues for 9 floors! On the first two floors you will find mechanics, electronic components, measurement equipment, leds, cabling… The list just goes on, they even had a small pick and place machine for prototype batches. Continuing upwards it becomes more and more computer hardware like graphics cards, mother boards, memory and hard-drives. These floors also have stuff like routers, cameras and tablets. Going even higher up everything is put together and you can buy laptops and computers. Its really amazing the diversity of things you can find, we even saw some cashier machines. Walking from the bottom floor upwards we really got the feeling that as you get higher things get more and more assembled. And everything is very cheap, for example we bought 300 pogo-pins in different variations for 100 yen (~16 USD), but expect the quality to be there after.
So what did we end up buying? Well, lots of stuff! We bought a lot of prototype stuff that we will use for the Crazyflie like cables, antennas, screws and batteries. And we also found a really nice USB microscope with a stand that does 500x magnification :-)
We uploaded some photos to our Picasa album for Seeed/Shenzhen.
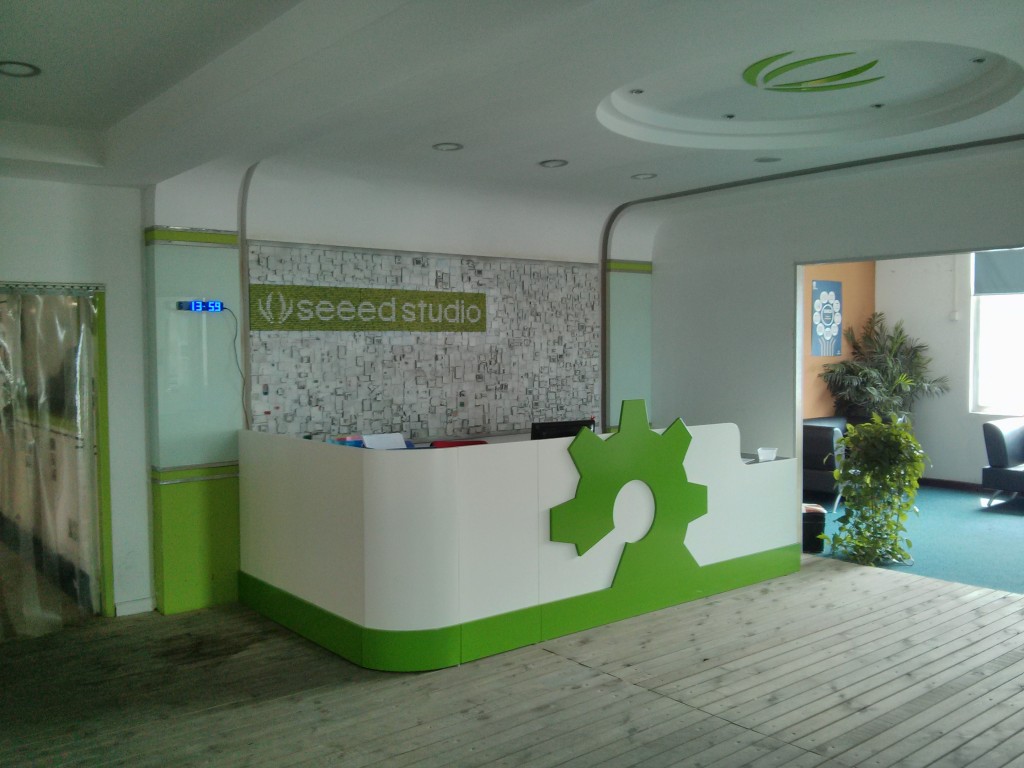